NanoAndMore GmbH does not ship to your country
Force Modulation (FM) AFM Probes
AFM probes in this category bridge the gap between probes for contact mode and non-contact mode AFM applications. With their intermediate force constant of a few N/m these AFM probes can be used for both modes – contact mode as well as non-contact or tapping mode AFM. Their main field of application is measurement and visualization of local variations in sample stiffnesses, but they are also used for soft-tapping mode AFM, which is used for mapping the surface topography of soft material samples.
AFM provides several techniques for measuring AFM tip-sample forces. A method that is implemented into almost each AFM instrument is based on force distance curves. For this method, usually called Force Spectroscopy, the xy-scan is stopped and the cantilever reaction to a vertical AFM probe movement at the current location is recorded. Typically, the curve covers the movement of the AFM tip from a certain distance above the surface as well as a portion where the AFM tip touches the surface while the actuator moves down further. The curve contains a lot of information about material properties as adhesion, stiffness (modulus of elasticity) and rupture force but extracting data relies on application of complex models and a detailed knowledge about the AFM tip shape and mechanical properties of the specific AFM probe used.
State-of-the-art AFM instruments allow surface mappings based on the same concept. Force distance curves are automatically performed at each mapping point. Sometimes, the method is combined with automated extraction of certain parameters in order to enable visualization of local differences in mechanical sample properties. Usually, the approach-retract cycle is done by linear movement, but it could be done by a harmonic movement below the AFM cantilever resonance frequency, as well, if results are subsequently linearized.
Another method for visualization of mechanical sample properties is called Force Modulation Mode. It is based on a contact mode feedback scheme where the AFM tip-sample force is kept constant during scanning. The feedback loop detects changes in AFM cantilever deflection and adjusts the z-position to keep AFM cantilever deflection and, thus, AFM tip-sample forces constant. This basic scheme is supplemented by an additional modulation of the vertical AFM probe position. By that, the AFM tip-sample forces are modulated, and the deflection signal is a composition of a direct current (DC) and an alternating current (AC) signal. The DC deflection signal is used for contact mode feedback and corresponding surface reconstruction. The AC part of the deflection signal corresponds to the local stiffness of the sample under investigation and allows the detection of different mechanical properties within the sample surface.
For most samples investigated by these methods the intermediate force constant of Force Modulation AFM Probes is important as a compromise between force sensitivity and stability. The force constant must be large enough to enable modulations of the surface topography but soft enough for sufficient force sensitivity. AFM probes within this category are usually the best choice.
However, in case of very soft sample materials, AFM cantilevers with lower force constant (constant mode AFM probe type) should be used and in the case of very hard samples, AFM probes with larger force constant are necessary. In the latter case, AFM probes with hardened AFM tip should be used to avoid AFM tip breakage during the experiment (see Hardened / Enhanced Wear Resistance AFM Probes).
Often these techniques are combined with AFM tip functionalization, for obtaining insights into specific interactions on molecular level, e.g. within antigen-antibody-bindings. For that, the AFM tip is coated with one specimen while the other one is fixed to a sample surface. Afterwards, the force spectroscopic method can be applied and reveals binding characteristics such as the rupture force. The AFM tip functionalization is very specific for the experiment and, usually, not stable over time. Therefore, these kinds of modifications are typically done by AFM scientists just before performing an experiment.
Combined with specific AFM tip coatings, Force Modulation AFM Probes are also used as basis for other application modes such as Electrical Force Microscopy (EFM), Kelvin Probe Force Microscopy (KPFM) or Magnetic Force Microscopy (MFM). Such AFM probes with AFM tip side metallization are provided by different manufacturers. (see Conductive AFM Probes, Magnetic AFM Probes).
AFM probes for Force Modulation Mode and Force Spectroscopy are manufactured with different AFM tip shapes and optional reflective coatings. The AFM tip shape should be selected carefully as trade-off between achievable lateral resolution and rigidity during experiment. The AFM tip-sample forces are typically higher than those applied in topography measurement modes and AFM tip stability during the experiment is crucial for reliable results. Soft materials can be investigated by using sharp high aspect ratio AFM tips, samples of intermediate hardness require AFM tips with lower aspect ratio and hard samples require usage of hardened AFM tips (see Hardened / Enhanced Wear Resistance AFM Probes).
Force Modulation AFM Probes provide unrivaled flexibility in use and serve as basis for several application modes beyond basis topography imaging.

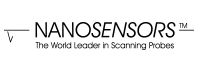
Tip Shape: Visible
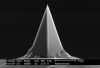
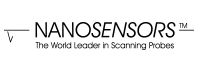
Tip Shape: Standard
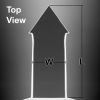
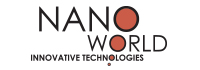
Tip Shape: Arrow
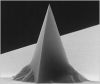
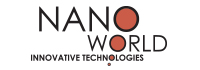
Tip Shape: Standard
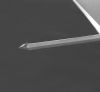
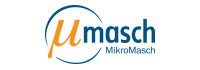
Tip Shape: Rotated
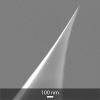
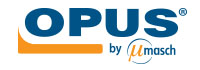
Tip Shape: Optimized Positioning
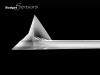
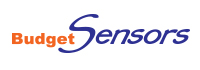
Tip Shape: Rotated
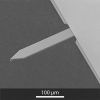
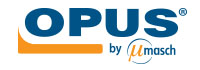
Tip Shape: Optimized Positioning
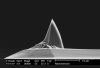
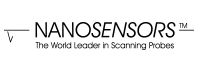
Tip Shape: Rotated
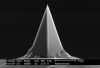
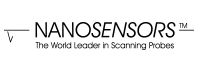
Tip Shape: Standard
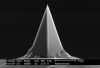
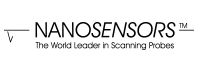
Tip Shape: Standard
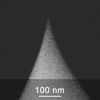
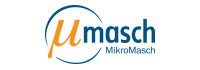
Tip Shape: Rotated
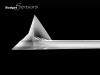
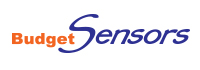
Tip Shape: Rotated
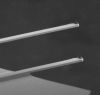
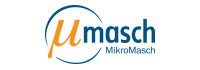
Tip Shape: Rotated
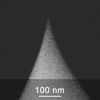
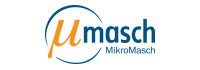
Tip Shape: Rotated
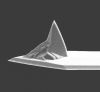
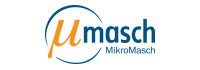
Tip Shape: Rotated
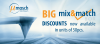
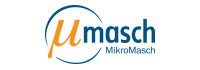
Tip Shape: various
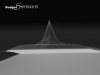
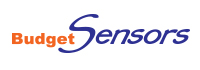
Tip Shape: Rotated
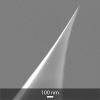
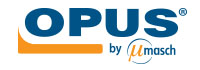
Tip Shape: Optimized Positioning
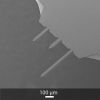
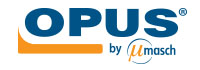
AFM Probe with 3 Different AFM Cantilevers for Various Applications and AFM Tips at the Very End of the AFM Cantilevers
Tip Shape: Optimized Positioning